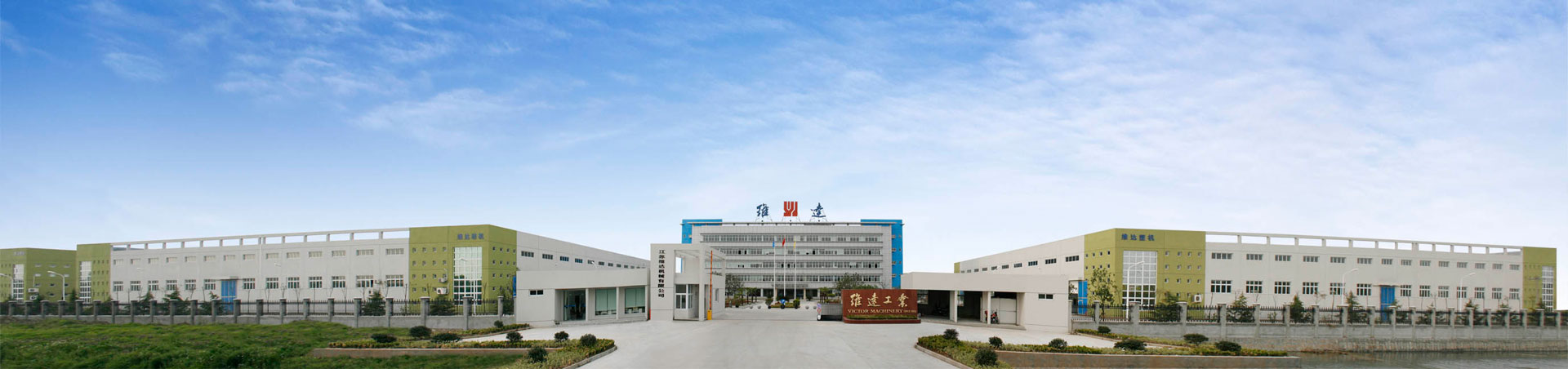
Technical Features
Both injection and blowing stations adopt three cylinder mold locking structure, open and close the mold fast, shorten production cycle with high efficiency.
Servo double oil hydraulic drive system with accurate control, energy saving more than 25%.
The triangular beam structure has high rigidity and good stability.
Linear guide for barrel movement, low resistance, high precision.
Stripping plate overturn pneumatically, safe and clean.
Strong versatility, compatible with MSZ60 mold.
Servo double oil hydraulic drive system with accurate control, energy saving more than 25%.
The triangular beam structure has high rigidity and good stability.
Linear guide for barrel movement, low resistance, high precision.
Stripping plate overturn pneumatically, safe and clean.
Strong versatility, compatible with MSZ60 mold.
Optional
Electric preplasticizing, synchronous plasticizing can be realized.
Electric stripping, energy saving and clean.
Electric table rotation, high precision of rotation positioning.
Product Application
Advantage
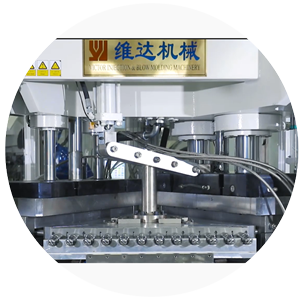
Special designed single crossbar dual-cylinder balance clamping system,for fast opening and closing mold while ensuring uniform distribution.
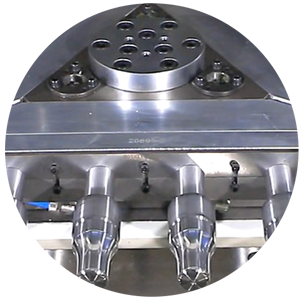
Unique rotating mechanism design, and equipped with automatic lubrication system,ensure rotation precision be consistent.
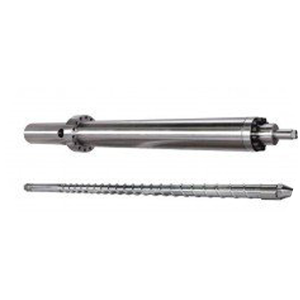
Alternative efficient plasticizing mixing screw, optimization of the injection unt,improve the injection stability and accuracy.

Equipped with electro-hydraulic servo system, the machine is running stable, low noise, high response and energy saving of 25% to 45%.
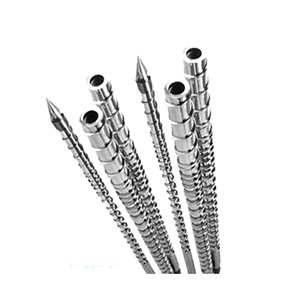
Screw optimization design, clamp screw head assembly, with good plasticizing ability, wear resistance.
Processing principle
Injection blow molding machine has an accurate three-station rotary table design.After preform injection, the preform will be rotated to blow station and bottle forming, finally bottle rotated to stripping station.The bottles can be packaged directly or transported by conveyor to the next process.Because of the precise design of the mold, the I.B.M bottle has perfect neck, precise dimension, uniform wall thickness, which can meet high standard packaging needs of pharmaceutical, chemical, cosmetic and food packing industry.The I.B.M is suitable for PE, PP,PS, SAN, EVA, COC, PEEL, TPU, PETG, PLA etc material, bottle volume various from 1ml-1000ml.It is a professional equipment for high-efficiency packaging manufacturing.
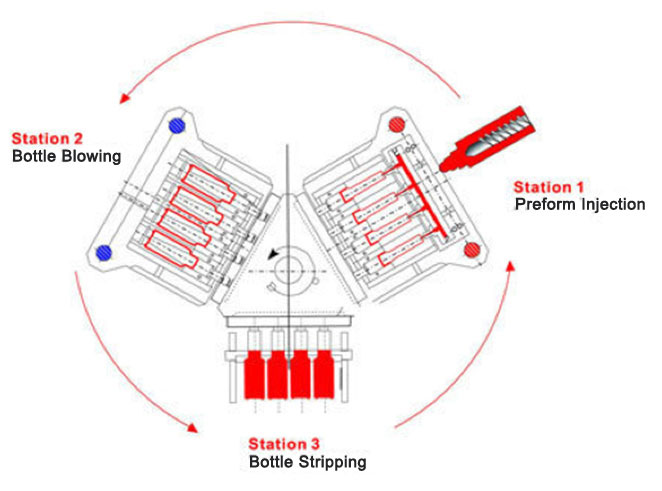
Parameter Table
Technical Parameters | |||
Preform system | Unit | MSZ70AE | |
Screw diameter | mm | 50 | 55 |
Screw L/D | L/D | 23:1 | 23:1 |
Shot volume | cm3 | 392 | 475 |
Injection weight(HDPE) | g | 372 | 450 |
Max.Screw speed | rpm | 10-300 | |
Heating capacity | KW | 10.8 | |
No.of heating zone | Qty | 3+N | |
Clamping system | |||
Clamping force of preform | KN | 750 | |
Clamping force of blowing | KN | 89 | |
Opening stroke of mold planten | mm | 140 | |
Lifting H of rotary table | mm | 70 | |
Max.Platen size(L×W) | mm | 800×390 | |
Min.mold thickness(H) | mm | 280 | |
Heating capacity of mould | KW | 6 | |
Stripping system | |||
Stripping stroke | mm | 230 | |
Dry cycle | sec | 2.1 | |
Driving system | |||
Motor power | KW | 5-800 | |
Hydraulic pressure | Mpa | ≤200 | |
Product range | ≤100 | ||
Suitable bottle range | ml | ||
MAX.bottle height | mm | 1 | |
Max.Dia.of bottle | mm | ≥0.8 | |
Other | 5 | ||
Min.air pressure | Mpa | 73.8 | |
Discharge rate of compressed air | m3/mm | 5.02×1.95×2.49 | |
Water flowage | m3/h | 9.3 | |
Total rated power with mold heating | KW | MSZ70AE | |
Dimension(L×W×H) | M | 50 | 55 |
Net weinght | ton | 23:1 | 23:1 |